Precision Plastic Injection Molding: Transforming Manufacturing with Excellence
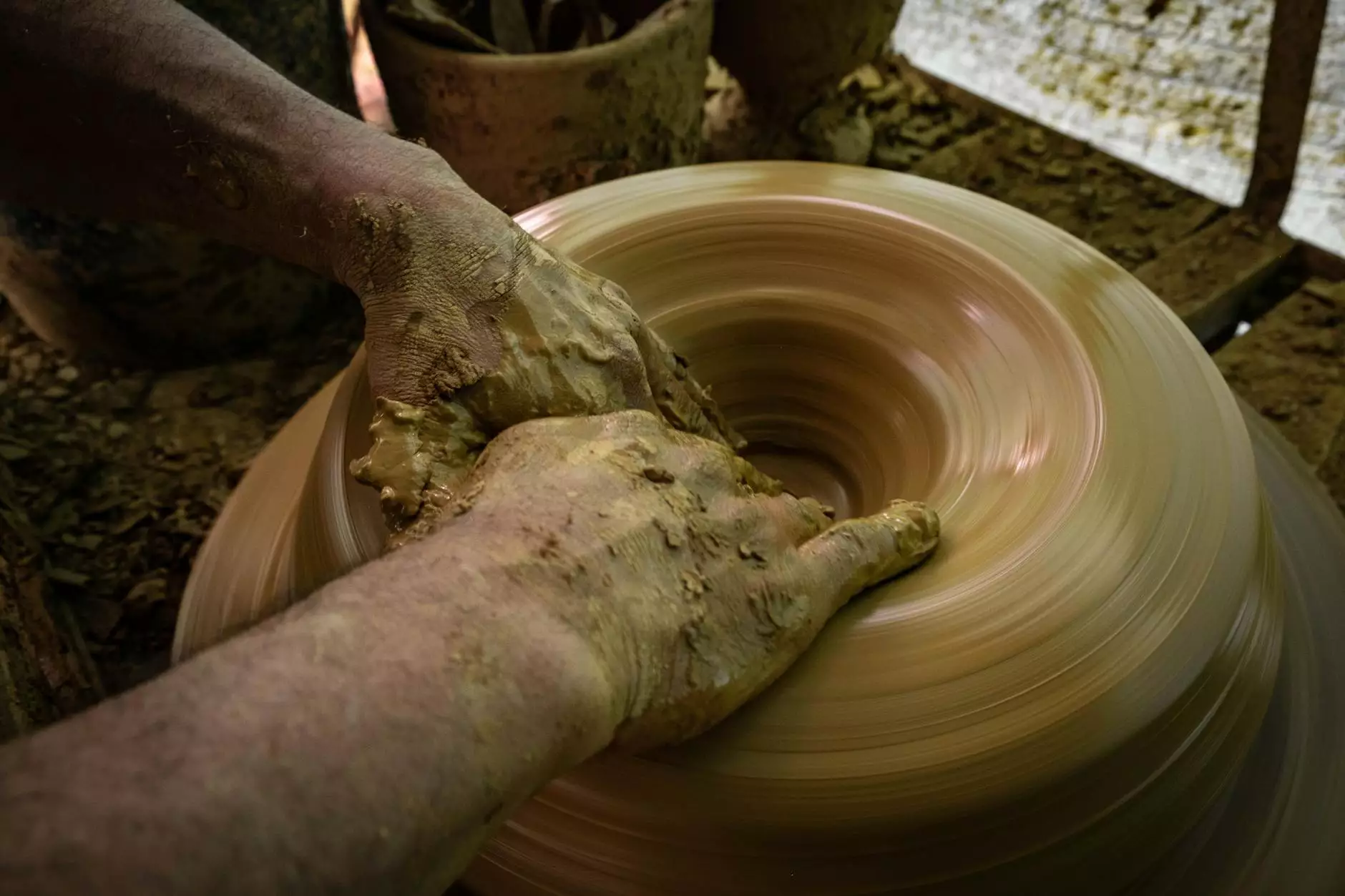
The world of manufacturing is continuously evolving, and one of the most significant advancements that have shaped modern production processes is precision plastic injection molding. This innovative technique not only enhances the efficiency of manufacturing but also ensures that products meet the highest quality standards. In this article, we will delve into the intricacies of precision plastic injection molding, its benefits, applications, and why it is the preferred choice for many manufacturing industries.
Understanding Precision Plastic Injection Molding
Precision plastic injection molding is a manufacturing process used for producing parts by injecting molten material into a mold. This method is best suited for the mass production of complex shapes and designs, making it a go-to solution for a variety of industries including automotive, consumer goods, medical devices, and electronics.
The Process of Plastic Injection Molding
The process consists of several key steps:
- Material Selection: The first step involves selecting the appropriate thermoplastic material, which can vary based on the desired properties of the final product.
- Mold Design: Engineers create precise molds that outline the specifications of the desired component.
- Heating: The selected plastic material is melted to a liquid state using high temperatures.
- Injection: The molten plastic is injected into the mold under high pressure to ensure it fills every cavity.
- Cooling: The injected plastic cools and solidifies, forming the desired shape.
- Ejection: Once cooled, the mold opens, and the finished product is ejected.
Key Advantages of Precision Plastic Injection Molding
Companies are increasingly adopting precision plastic injection molding due to its numerous benefits, which include:
- High Efficiency: The process is designed for high-volume production, which significantly reduces cycle times and labor costs.
- Cost-Effectiveness: Over time, the initial investment in molds is offset by the low per-unit cost of mass production.
- Accuracy and Precision: This method allows for tight tolerances, making it suitable for complex and intricate designs.
- Versatility: A wide variety of materials can be used, including different types of plastics, allowing customization based on project needs.
- Minimal Waste: The process is designed to be efficient with minimal scrap material, making it eco-friendly.
Applications of Precision Plastic Injection Molding
The versatility of precision plastic injection molding is evident across various sectors. Here are some of the primary applications:
Automotive Industry
In the automotive sector, this process is crucial for creating components such as dashboards, door panels, and exterior trims. The ability to produce lightweight yet durable parts enhances vehicle performance and fuel efficiency.
Consumer Goods
From household appliances to packaging materials, precision plastic injection molding is integral in manufacturing components that are both aesthetically pleasing and practical for everyday use.
Medical Devices
The medical field relies heavily on this technology to produce intricate surgical instruments, drug delivery devices, and diagnostic equipment with the utmost precision necessary for patient safety.
Electronics
In electronics, plastic housings and components must be produced to exacting specifications to ensure performance and reliability. Precision plastic injection molding provides that needed precision.
Choosing a Reliable Manufacturer for Precision Plastic Injection Molding
When selecting a manufacturer for your precision plastic injection molding needs, consider the following factors:
- Experience: Look for manufacturers with a proven track record in the injection molding industry.
- Capabilities: Ensure they have the technological capabilities to handle your specific requirements.
- Quality Assurance: Reliable manufacturers employ strict quality control measures to meet industry standards.
- Customer Service: Good communication and support are vital for smooth project execution.
Future Trends in Precision Plastic Injection Molding
As technology advances, the future of precision plastic injection molding is poised for exciting developments. Key trends include:
Automation and Robotics
The integration of robotics in the injection molding process increases efficiency and reduces labor costs. Automated systems can rapidly produce complex parts with consistent quality.
Sustainable Practices
Awareness of environmental impacts is driving manufacturers towards sustainable practices. This includes the use of recycled materials and energy-efficient molding processes.
3D Printing Integration
The combination of traditional injection molding with 3D printing is revolutionizing prototyping and production, allowing for faster iterations and lower costs.
Conclusion
Precision plastic injection molding stands as a cornerstone of modern manufacturing, providing unparalleled efficiency, accuracy, and versatility. Its applications span numerous industries, adapting to the diverse needs of both manufacturers and consumers. As we continue to innovate and improve manufacturing processes, the significance of precision plastic injection molding is only set to grow, cementing its role in shaping the future of production.
For businesses looking to leverage the benefits of precision plastic injection molding, partnering with industry experts such as DeepMould.net ensures access to cutting-edge technology and services tailored to meet specific production needs. Embrace the future of manufacturing with precision and excellence!