Understanding the Parts of CNC Lathe for Metal Fabrication
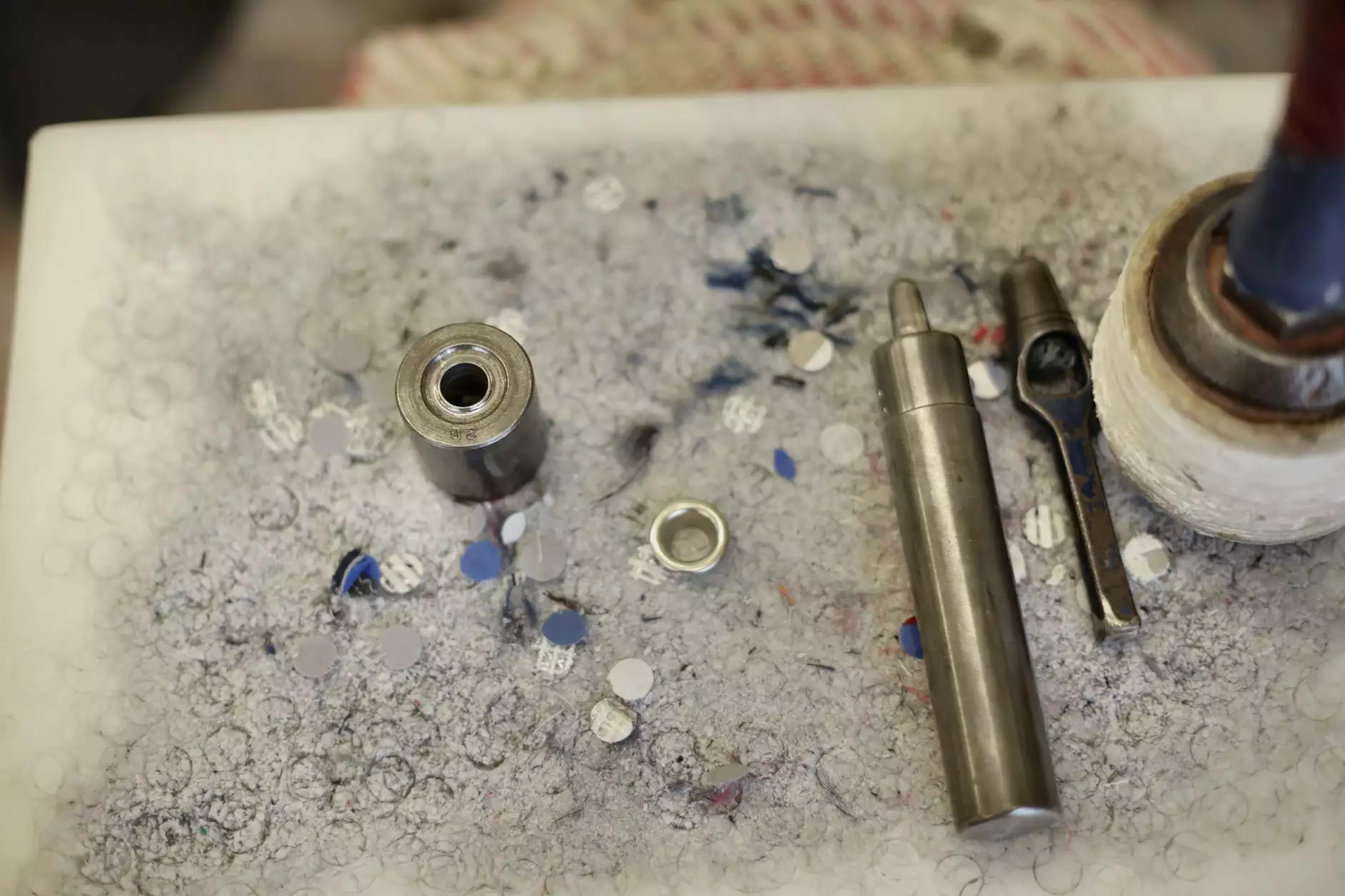
The realm of metal fabrication has evolved significantly over the years, owing largely to advancements in technology. One of the most transformative innovations in this field is the Computer Numerical Control (CNC) lathe. Understanding the various parts of CNC lathe machines is essential for anyone involved in modern manufacturing. This article delves into these components, their functionalities, and their significance in achieving precision in metalwork.
What is a CNC Lathe?
A CNC lathe is a type of machine tool that uses computer-controlled movements to shape materials. Unlike traditional lathes, CNC lathes are operated via software that dictates the movements of the machine, offering unparalleled precision and consistency. These machines are crucial in various sectors, including automotive, aerospace, and general metalworking.
Key Components of CNC Lathes
The parts of CNC lathe machines are intricately designed to ensure efficient operation. The following are the primary components:
- Bed: The bed is the foundation of the lathe, providing stability and support for the other components. It is typically made of cast iron, which absorbs vibrations and enhances machining accuracy.
- Headstock: This component houses the main spindle and control mechanisms. The headstock is responsible for holding the workpiece and rotating it during machining.
- Tailstock: Opposite the headstock, the tailstock supports the other end of the workpiece. It can be adjusted to accommodate different lengths of material.
- Carriage: The carriage moves along the bed and controls the movement of the cutting tool. It includes several crucial parts such as the cross slide and tool post.
- Tool Post: Located on the carriage, the tool post holds the cutting tools. It can be adjusted to change the angle or position of the tool for different cuts.
- Spindle: The spindle is the rotating axis of the lathe that holds and drives the workpiece. Its speed and torque can be controlled through the CNC software.
- Control Panel: This is the interface where the operator inputs commands into the CNC system. It often includes a screen, keypad, and various buttons for controlling machine functions.
- Live Tooling: Some advanced CNC lathes come equipped with live tooling capabilities, allowing for drilling and milling at the same time as turning.
Advantages of CNC Lathes
The transition from manual lathes to CNC lathes offers numerous advantages, particularly in the field of metal fabrication. Here are some key benefits:
- Precision: CNC lathes produce parts with a high degree of accuracy, reducing the margin for error.
- Consistency: Once programmed, CNC lathes can produce identical parts with minimal variation.
- Automation: CNC technology reduces the need for manual labor, allowing operators to focus on monitoring machines rather than manually adjusting them.
- Complex Shapes: CNC lathes can create intricate designs that would be impossible to achieve with manual machining.
- Flexibility: The software can be easily modified to accommodate changes in part design or production runs.
Common Applications of CNC Lathes
CNC lathes are widely utilized across various industries, showcasing their versatility. Some common applications include:
- Automotive Parts: Producing components such as shafts, bushings, and fittings.
- Aerospace Components: Manufacturing critical components that require high precision and durability.
- Medical Devices: Creating small, precise parts for medical instrumentation and devices.
- General Manufacturing: Producing a wide range of parts for different applications in engineering and manufacturing sectors.
Maintenance of CNC Lathes
Maintaining the various parts of CNC lathe machines is essential for ensuring their longevity and performance. Here are some maintenance tips:
Regular Cleaning
Keeping the machine clean is crucial. Regularly remove chips, dust, and contaminants to prevent damage and ensure smooth operation.
Lubrication
Ensure that all moving parts are lubricated according to the manufacturer's recommendations. Proper lubrication reduces wear and supports smooth movements.
Calibration
Regularly calibrate the CNC machine to maintain accuracy. Check and adjust the tool offsets and the alignment of components.
Inspection
Conduct routine inspections of all parts, including the bed, headstock, tailstock, and the tool post. Look for signs of wear or damage and address any issues promptly.
The Future of CNC Technology
As technology continues to advance, the capabilities of CNC lathes are expected to grow. The integration of artificial intelligence and machine learning into CNC operations may lead to further improvements in efficiency and productivity. Future CNC lathes are likely to feature enhanced automation, predictive maintenance capabilities, and improved user interfaces.
Conclusion
Understanding the parts of CNC lathe machines is vital for anyone in the field of metal fabrication. As the manufacturing landscape evolves, being knowledgeable about these machines not only improves productivity but also opens up new possibilities for innovation. With benefits such as precision, automation, and flexibility, CNC lathes are paving the way for the future of manufacturing.
For those looking to stay ahead in the metal fabrication industry, investing in CNC lathe technology is a step toward ensuring quality and efficiency in production. If you want to learn more about CNC lathes and their applications in modern manufacturing, consider exploring resources and tutorials available online.
For additional information and professional services, visit deepmould.net.