The Ultimate Guide to Plastic Injection Molding Manufacturing
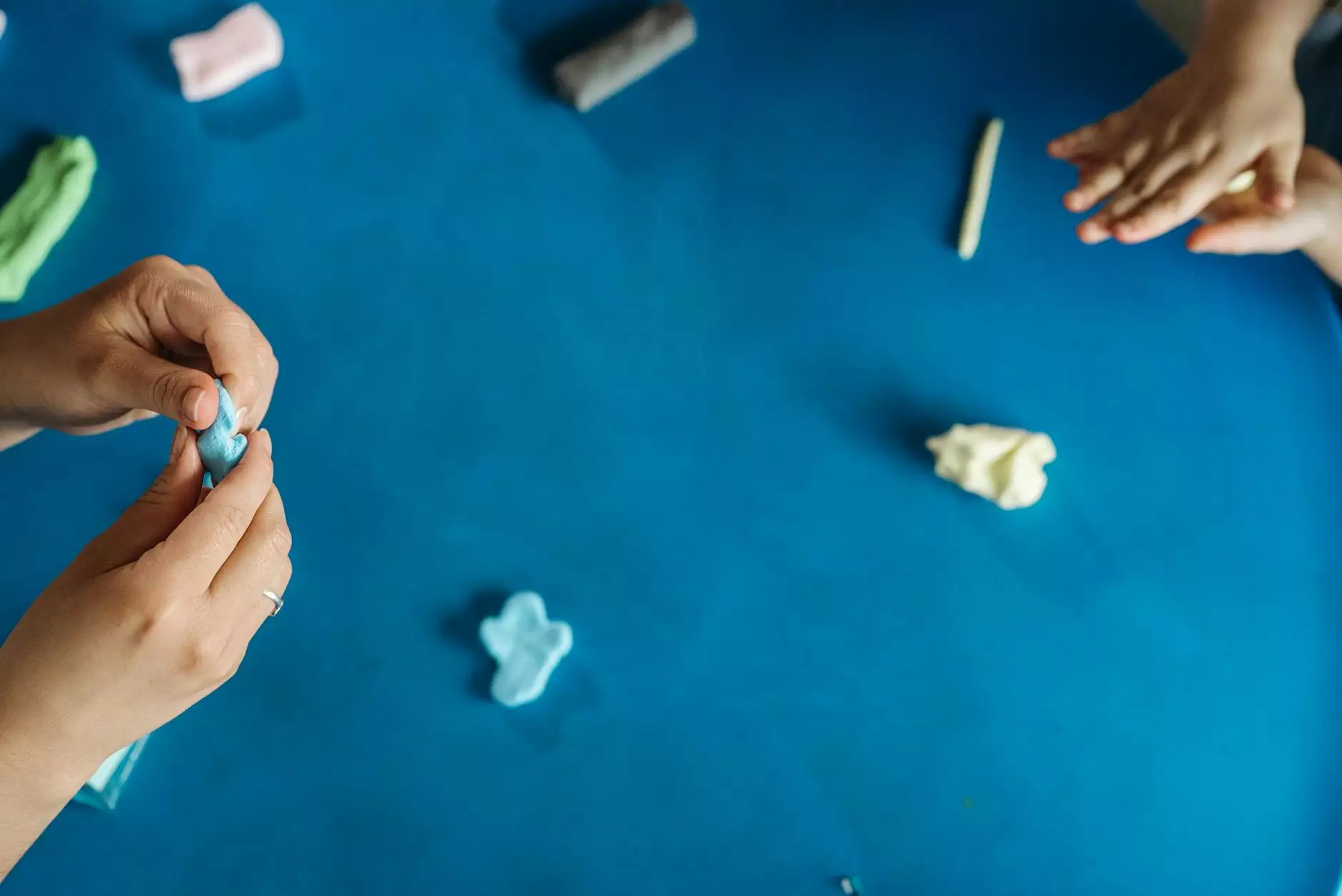
Plastic injection molding is a process that has revolutionized the manufacturing industry, allowing for the mass production of intricate designs and components from plastic materials. As a leading plastic injection molding manufacturer, Deep Mould embodies the essence of innovation, precision, and reliability, catering to various sectors, including but not limited to electronics, automotive, and consumer products. In this comprehensive guide, we will delve into the intricacies of plastic injection molding, its advantages, applications, and why choosing the right manufacturer is crucial for success.
Understanding Plastic Injection Molding
Plastic injection molding is a manufacturing process that involves injecting molten plastic into a mold cavity. This method allows for the replication of complex shapes and designs with high precision. The process begins with heating plastic pellets until they melt, followed by injecting this molten plastic under high pressure into a cooled mold. Once the plastic cools and solidifies, the mold opens, and the finished part is ejected.
The Steps of the Plastic Injection Molding Process
- Material Selection: Choosing the right type of plastic resin is crucial for the desired properties of the final product.
- Designing the Mold: The mold is designed to meet exact specifications, a vital step that influences production efficiency and quality.
- Heating and Injection: The resin is heated to its melting point and injected into the mold.
- Cooling and Solidification: The molten plastic is cooled to solidify, allowing it to take the shape of the mold.
- Mold Removal: The mold opens, and the finished product is ejected.
Advantages of Plastic Injection Molding
There are numerous advantages to using plastic injection molding that solidify its position as a preferred manufacturing technique:
- High Efficiency: Once a mold is created, the time to produce each part is minimized, making it a quick process for large production runs.
- Cost-Effective for Mass Production: The initial costs can be high due to mold creation, but the per-unit cost decreases significantly with increased production volumes.
- Design Flexibility: Complex shapes and designs can be produced with precision, offering extensive customization options.
- Material Variety: A wide range of thermoplastics and some thermosetting plastics can be used, broadening the application scope.
- Improved Mechanical Properties: The final products often demonstrate enhanced mechanical strength, stability, and durability.
Applications of Plastic Injection Molding
As a versatile manufacturing method, plastic injection molding serves a multitude of industries:
1. Automotive Industry
Manufacturers produce various components such as dashboards, bumpers, and interior trims, showcasing the process's ability to create durable and lightweight parts.
2. Consumer Goods
Items ranging from kitchenware to toys are manufactured using injection molding, allowing for vibrant colors and intricate designs.
3. Electronics
Plastic parts in devices such as smartphones and computers require precision and durability, making injection molding ideal for creating casings and components.
4. Medical Supplies
The healthcare industry relies on injection molding for creating medical devices and disposable products that demand high hygiene and consistency standards.
5. Packaging
Injection molding is used to create various packaging solutions, including containers, lids, and packaging components, emphasizing functionality and aesthetic appeal.
Choosing the Right Plastic Injection Molding Manufacturer
Selecting the right plastic injection molding manufacturer is critical for achieving successful outcomes in your projects. Here are several factors to consider:
1. Experience and Expertise
Look for manufacturers with a proven track record and extensive knowledge in the field. Deep Mould, for instance, has years of experience in delivering quality solutions.
2. Technological Capabilities
The manufacturer should utilize the latest technology in machinery and processes to ensure precision and efficiency. Cutting-edge equipment can significantly improve production timelines and reduce wastage.
3. Customization Options
The ability to customize various aspects, from the type of materials to the complexities of designs, is crucial. A flexible manufacturer can cater to unique project requirements.
4. Quality Assurance Processes
Effective quality control measures should be in place to ensure that every part meets the highest standards. This includes regular inspection and testing of products.
5. Competitive Pricing
Evaluate the pricing structures. While quality often costs more, a good manufacturer will offer a balance between affordable pricing and exceptional service.
Deep Mould: Your Premier Plastic Injection Molding Manufacturer
At Deep Mould, we pride ourselves on being a leading plastic injection molding manufacturer. Our commitment to excellence and customer satisfaction sets us apart. By leveraging advanced technologies and innovative practices, we ensure that our clients receive top-notch products tailored to their specific needs.
Why Partner with Deep Mould?
- Advanced Machinery: Our state-of-the-art technology guarantees we produce high-quality parts efficiently.
- Skilled Team: Our professionals are highly trained, ensuring every project is handled with care and precision.
- Comprehensive Services: From design to production, we offer end-to-end solutions that cover all your needs.
- Commitment to Sustainability: We prioritize eco-friendly materials and processes, reducing waste and promoting a sustainable future.
- Customer-Centric Approach: Your satisfaction is our priority. We listen to your requirements and adapt accordingly.
Future of Plastic Injection Molding
The future of plastic injection molding is promising, with numerous advancements on the horizon. Industry trends include:
1. Biodegradable Plastics
With increasing emphasis on sustainability, the use of biodegradable plastics in injection molding will rise, offering eco-friendly alternatives.
2. Smart Manufacturing
Integrating Internet of Things (IoT) technologies will allow for real-time monitoring of the injection molding process, enhancing efficiency and reducing downtime.
3. Enhanced Personalization
As consumer preferences evolve, manufacturers will leverage advanced customization techniques, allowing for more personalized products.
4. 3D Printing Integration
The synergy between 3D printing and injection molding will foster faster prototyping and development cycles, revolutionizing product design timelines.
Conclusion
In conclusion, the role of a plastic injection molding manufacturer in today’s manufacturing landscape cannot be overstated. With Deep Mould at the forefront, businesses can expect unparalleled quality, speed, and innovation. As we look to the future, the potential for advancements in this field is limitless, making it a key area for investment and growth. When considering your next project, trust in the expertise and capability of a reliable partner like Deep Mould to ensure your success.