Molding Plastic Injection: A Comprehensive Guide to Modern Manufacturing
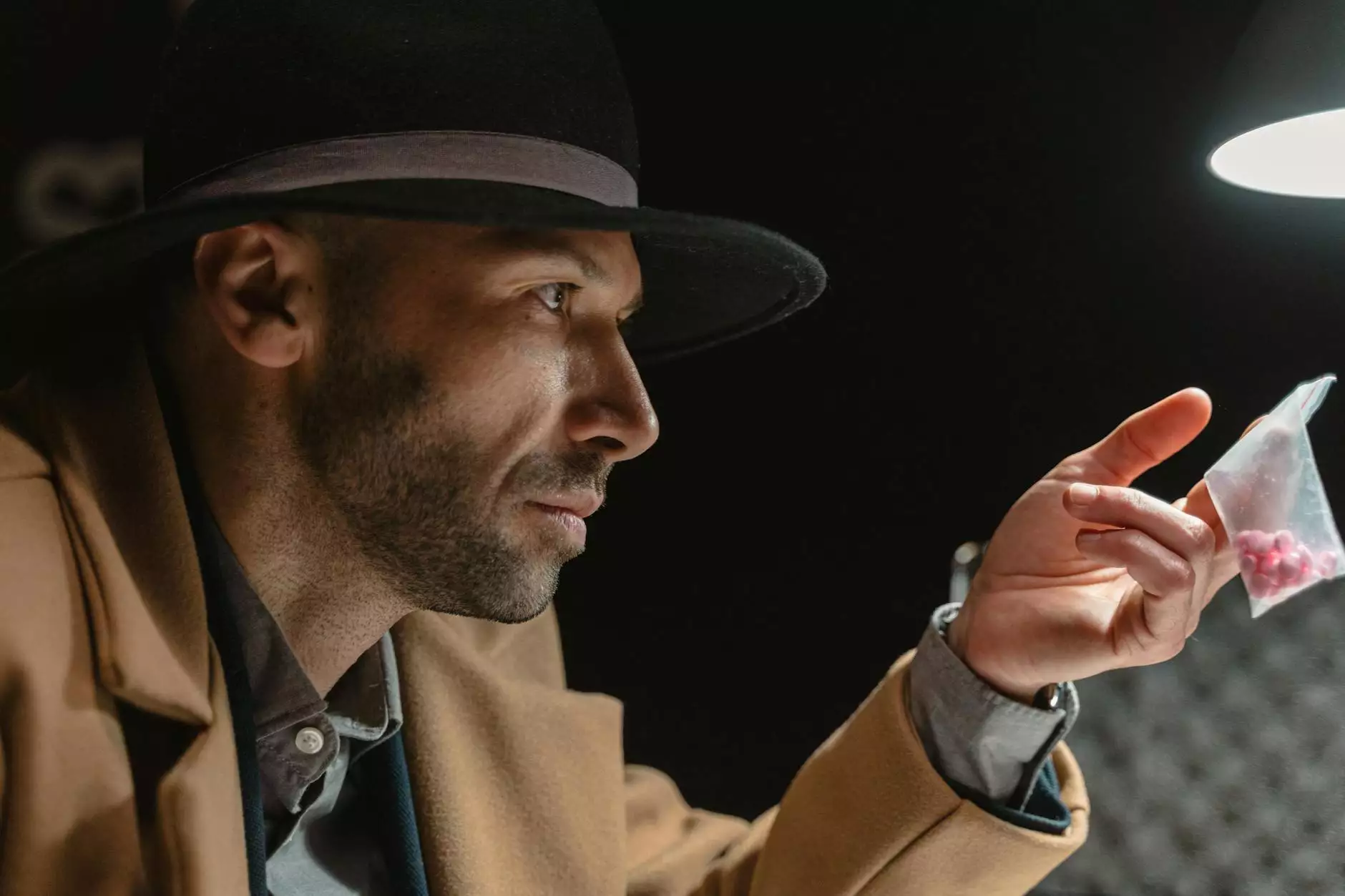
Molding plastic injection has become a pivotal process in the manufacturing industry, especially in sectors that require precision and efficiency in producing complex parts. As industries evolve, the demand for high-quality plastic components continues to rise, making injection molding a key player in meeting these demands. This article delves into the various aspects of molding plastic injection, targeting its significance in the metal fabrication industry and why businesses like Deep Mould are at the forefront of this innovation.
Understanding Molding Plastic Injection
At its core, molding plastic injection is a manufacturing process used to produce parts by injecting molten material into a mold. The process involves several critical stages:
- Material Preparation: Raw plastic pellets are fed into a hopper, where they are heated until they melt.
- Injection: The molten plastic is injected into a carefully designed mold under high pressure.
- Cooling: Once the mold is filled, the plastic cools and hardens, taking the shape of the mold.
- Ejection: The finished part is ejected from the mold, usually with the help of ejector pins.
This method allows for rapid production of high-precision parts, which can be made from various types of plastics, including thermoplastics and thermosets. The versatility and efficiency of this process are what make it indispensable in modern manufacturing.
The Advantages of Molding Plastic Injection
When considering molding plastic injection for manufacturing needs, it’s essential to recognize its numerous advantages:
- High Efficiency: The injection molding process allows for the rapid production of large quantities of parts, reducing manufacturing time significantly.
- Complex Geometries: Injection molds can produce intricate designs that would be challenging to achieve with other manufacturing processes.
- Minimal Waste: The process is highly material-efficient, using only the necessary amount of plastic and minimizing scrap.
- Cost-Effective for Mass Production: While the initial setup cost for molds can be high, the long-term savings in labor and material costs make it economical for large runs.
- Diverse Material Compatibility: A wide variety of plastics can be used, each with its unique properties, allowing for more tailored solutions for different applications.
Applications of Molding Plastic Injection
The versatility of molding plastic injection has led to its adoption across various industries. Here are some of the primary applications:
1. Automotive Industry
In the automotive sector, injection-molded components are crucial for producing lightweight and durable parts. Examples include:
- Dashboard panels
- Door handles
- Exterior trims
2. Household Goods
From kitchen utensils to storage containers, many everyday items are produced using molding plastic injection.
3. Electronics
Injection molding provides the precision necessary for electronic housings and components, enhancing both functionality and aesthetics.
4. Medical Devices
High-precision plastic parts for medical applications ensure reliability and compliance with strict regulatory standards.
Eco-Friendly Practices in Molding Plastic Injection
As environmental awareness grows, the plastic molding industry is also adapting by implementing eco-friendly practices. Companies like Deep Mould are advocating for the use of recyclable materials and sustainable processes. Some initiatives include:
- Using Biodegradable Plastics: Innovations in materials science have led to the development of biodegradable alternatives that serve various applications.
- Energy-efficient Machinery: Investing in state-of-the-art equipment that consumes less energy during the molding process.
- Closed-Loop Recycling: Implementing systems that recycle plastic waste back into the production process, reducing landfill contributions.
Choosing the Right Molding Plastic Injection Partner
When selecting a partner for your plastic injection molding needs, consider the following factors to ensure you achieve optimum results:
1. Experience and Expertise
Look for manufacturers with a proven track record in the industry. Experience translates into a better understanding of complex challenges and efficient solutions.
2. Advanced Technology
Inquire about the machinery and software technologies the manufacturer employs. Cutting-edge technology can significantly impact quality and efficiency.
3. Material Options
Assess the range of materials that a manufacturer is capable of working with. They should offer various plastic types that suit your specific application requirements.
4. Quality Assurance Processes
A reputable manufacturer will have stringent quality control measures in place. Ensure they follow recognized standards and regularly conduct inspections.
5. Customization Capabilities
Your partner should be capable of providing tailored solutions, from design adjustments to initial prototypes. Flexibility is crucial in meeting unique demands.
The Future of Molding Plastic Injection
The future holds exciting prospects for the molding plastic injection industry. Advancements in technology, such as automation and artificial intelligence, are set to further enhance productivity and innovation. Additionally, as industries push for sustainability, the development of new materials and recycling methods will play a crucial role in shaping the future of manufacturing.
Conclusion
In conclusion, molding plastic injection is undeniably a significant force in modern manufacturing. Its advantages in efficiency, versatility, and precision make it a vital process, particularly in the metal fabrication sector. By choosing a reliable partner like Deep Mould, businesses can leverage cutting-edge technology and expertise to achieve high-quality products that meet today’s demands, while also embracing sustainable practices that will benefit future generations.
Understanding this manufacturing process, its applications, and its advantages equips businesses with the knowledge to make informed decisions. As you consider your options, remember the crucial role that quality partners and progressive practices play in the realm of manufacturing.